Laser welding
Laser welding (LW) is a welding technique used to join pieces of metal or thermoplastics through the use of a laser. The beam provides a concentrated heat source, allowing for narrow, deep welds and high welding rates. The process is frequently used in high volume applications using automation, as in the automotive industry. It is based on keyhole or penetration mode welding. It can join work pieces at the surface or create deep weld seams.
ICE trains, transmission parts of cars and trucks, airbag sleeves, pacemakers - laser weld seams and weld spots can be found in a wide variety of places. Hardly any tool is more versatile than the laser: It can be used to produce fine weld spots of one millimeter in diameter as well as meter-long, deep-welded seams very quickly. In the process, very slim seam geometries with a large depth-to-width ratio are produced with minimal distortion. Lasers weld materials with both high melting temperatures and high thermal conductivity. Because of the small melt and the short, controllable melting time, they can sometimes even join materials that are otherwise impossible or difficult to weld.
Advantages
- Distortion Free
- Very Good Joint Strength
- Very Small HAZ
- Aesthetic Welds
- In most cases no filler wire required.
Laser Welding on Heat exchangers

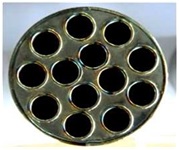
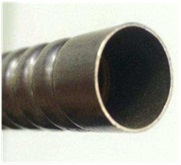
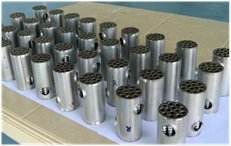
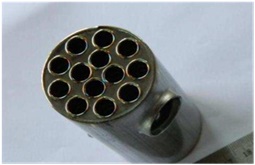
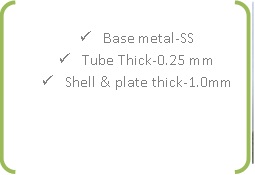